Membraaninstallatie dikt kaaswei in voor transport
De uitdaging bij de installatie van de membraaninstallatie voor het indikken van wei bij FrieslandCampina Gerkesklooster was de flexibele planning. De investering kwam na de nieuwbouw van het kaaspakhuis en de herbouw van het pekelgebouw na een brand vijf jaar geleden.
Tekst: Yves De Groote
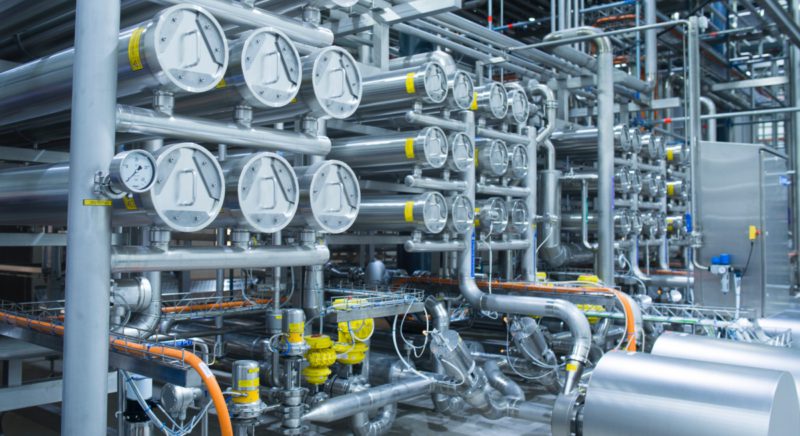
De omgekeerde osmose-membraaninstallatie verwerkt wei van koe- en geitenmelk. (Foto: Robert Huurneman)
De moderne kaasfabriek van FrieslandCampina in Gerkesklooster is uit de as herrezen. Bij de zware brand in 2014 gingen het kaaspakhuis geheel en het pekellokaal gedeeltelijk verloren. Meteen na de nieuwbouw van het kaaspakhuis en de herbouw van het pekelgebouw werden plannen gemaakt om niet alleen de productie zo snel mogelijk te hervatten, maar ook de productiecapaciteit te verdubbelen, zegt technisch projectmanager Henk Jonkman. Dit hield in dat naar het ontwerp van alle installaties zorgvuldig gekeken moest worden, in het bijzonder voor het indikken van de wei van de koe- en geitenmelk.
Membraaninstallatie
In de zoektocht naar een nieuwe membraaninstallatie, voor het indikken van wei afkomstig van koemelk en geitenmelk, was er contact met vier leveranciers. “Alleen Alpma had heel wat kennis van en voldoende ervaring met membraantechnologie voor het concentreren van beide weisoorten”, blikt Jonkman terug. “Dat werd al snel duidelijk tijdens het inkooptraject, wat meteen vertrouwen gaf voor de realisatie van het project.” Geitenmelk heeft een andere vetsamenstelling en wordt in tegenstelling tot koemelk niet ontroomd.
“Bovendien was het voor Alpma, in tegenstelling tot enkele andere leveranciers, geen probleem om enkele van hun standaardcomponenten in te wisselen voor voorkeurcomponenten van FrieslandCampina. Deze machinefabrikant dringt niets op.” De loops voor de concentratiestappen in de installatie zijn op één na geleverd door de voorkeurleverancier van Alpma. “Op advies van onze R&D-afdeling is voor de laatste concentratiestap gekozen voor een membraan van een andere leverancier – geen probleem voor Alpma”, verduidelijkt Jonkman. “De leverancier houdt deze membranen op voorraad voor ons.” De kleppen in de installatie zijn de voorkeur van beide bedrijven. De voorkeurautomatiseringspartner in Gerkesklooster mocht de besturing van de membraaninstallatie voor zijn rekening nemen.
Engineering
Een snelle en flexibele verwerking van de melk was de rode draad in het state-of-the-artontwerp van de volledige kaasfabriek. Deze heeft een productiecapaciteit van circa 90.000 ton kaas per jaar op twee kaaslijnen, waarvan één is vernieuwd, vanwege de productie-uitbreiding. De verse wei van de nieuwe lijn is snel beschikbaar. “Dit is belangrijk voor de kwaliteit en voedselveiligheid van de wei, die verder wordt verwerkt”, onderstreept Jonkman.
Met uitzondering van de membraaninstallatie nam de kaasfabriek de engineering van de overige installaties in de kaasfabriek voor haar rekening. Jonkman: “De installatie van Alpma is de enige turnkeyinstallatie, waardoor deze leverancier verantwoordelijk is voor het ontwerp en de prestaties. We hebben deze keuze gemaakt, omdat deze omgekeerde (reverse) osmose-membraaninstallatie vijf jaar geleden relatief nieuw was voor het bedrijf.”
Voor de imposante installatie en de geconditioneerde ruimte voor de elektrische kast was een beperkt grondoppervlak beschikbaar. De membraaninstallatie, met een membraanoppervlak van 10.000 m2, is ontworpen om twintig uur per dag operationeel te zijn. Het CIP-proces is geoptimaliseerd.
De weiaanvoer uit de kaasfabriek wordt gescheiden in permeaat, zijnde puur water, en weiconcentraat. Het water wordt gebruikt in de CIP-installatie en voor de productie van stoom. Dit levert een forse besparing op.
Voor de gescheiden opslag van de aangevoerde wei van koe- en geitenmelk en het weiconcentraat zijn er verschillende opslagtanks. Vanuit Gerkes-klooster rijden dagelijks bulkvrachtwagens met wei naar de fabrieken van FrieslandCampina in Borculo en Veghel voor verdere verwerking tot hoogwaardige ingrediënten voor de voedings- en zuivelindustrie.
Uitdagingen
Naast de beperkte ruimte was de vereiste flexibiliteit van Alpma de voornaamste uitdaging bij het neerzetten van de membraaninstallatie. “De weekplanning kon van de ene op de andere dag veranderen met als gevolg dat de verschillende planningen van alle werkzaamheden optimaal op elkaar moesten worden afgestemd”, benadrukt Jonkman. Dit had te maken met het feit dat alle werkzaamheden voor de uitbreiding van de voorfabriek en de nieuwe kaaslijn de kaasproductie niet mochten storen. Samenwerking tussen alle betrokken partijen was geboden. Jonkman: “Alle installaties in de kaasfabriek moesten op elkaar aansluiten, zodat de productstroom weer door de fabriek kon lopen.”
Ontzorgen
De technisch projectleider van de kaasfabriek in Gerkesklooster laat weten dat de leverancier van de membraaninstallatie hier goed mee om wist te gaan. “Wietze Jongsma van Jongsma Engineering Solutions heeft zowel ons als Alpma, dat hij vertegenwoordigt, ontzorgd vanaf het eerste begin van het project tot en met de inbedrijfname van de membraaninstallatie. “Oplossingen werden dankzij een positieve professionele instelling – ‘afspraak is afspraak’ – telkens weer gezocht en gevonden. Directe en open communicatie – elkaar aanspreken als er iets niet goed gaat – is naast flexibiliteit en een goede persoonlijke relatie de voornaamste succesfactor om een project tot een goed eind te brengen.”
Dit artikel is verschenen in ZuivelZicht 12 2019. Nog geen abonnee? Klik HIER.